Plastic bottle manufacturing takes place in stages. Plastic bottle manufacturers generally use one of four types of plastic to create bottles. Typically, the plastic bottles used to hold potable water and other drinks are made from polyethylene terephthalate (PET), because the material is both strong and light.
Plastic Bottle
Plastic bottle manufacturing takes place in stages. Plastic bottle manufacturers generally use one of four types of plastic to create bottles. Typically, the plastic bottles used to hold potable water and other drinks are made from polyethylene terephthalate (PET), because the material is both strong and light. Polyethylene (PE) in its high-density form is used for making rigid plastic bottles such as detergent bottles and in its low-density form for making squeeze bottles. Polypropylene (PP) is used for pill bottles and the like. Polycarbonate (PC) is used for refillable water bottles and similar reusable containers.
What are Plastic Bottles Made of?
PET (Polyethylene Terephthalate)
Polyethylene Terephthalate is a thermoplastic polymer that can be either opaque or transparent, depending on the exact material composition. As with most plastics, PET is produced from petroleum hydrocarbons, through a reaction between ethylene glycol and terephthalic acid. The PET is polymerized to create long molecular chains, which allows it to produce PET bottles later on.
Polymerization itself can be a complicated process and accounts for many of the inconsistencies between one batch of manufactured PET and another. Typically, two kinds of impurities are produced during polymerization: diethylene glycol and acetaldehyde. Although diethylene glycol is generally not produced in high enough amounts to affect PET, acetaldehyde can not only be produced during polymerization but also during the bottle manufacturing process. A large amount of acetaldehyde in PET used for bottle manufacturing can give the beverage inside an odd taste.
Once the plastic itself has been manufactured, the PET bottle manufacturing process can begin. To ensure that the plastic is appropriate for use, numerous tests are done post-manufacturing to check that the bottles are impermeable by carbon dioxide (which is important for bottles that carry soda). Other factors, such as transparency, gloss, shatter resistance, thickness, and pressure resistance, are also carefully monitored.
LDPE/HDPE (Low- and High-Density Polyethylene)
Another thermoplastic, polyethylene is used for manufacturing blow-molded milk and water jugs, detergent bottles, ketchup bottles, spray bottles, and other products. Both LDPE and HDPE can be thermoformed, blow-molded, injection-molded, etc. LDPE was one of the first plastics to be blow molded and today it is still used for making squeezable bottles, as it has high ductility compared with HDPE, but lower strength. HDPE is used for many forms of pourable bottles. The material in its natural form is usually white or black and becomes translucent when thinned to the dimensions of milk bottles and the like. Suppliers can adjust formulation to increase tear strength, transparency, formability, printability, or other parameters.
Polyethylene is composed of a single monomer, ethylene, making it a homopolymer. LDPE is amorphous while HDPE is crystalline which accounts for LDPE’s greater ductility and HDPE’s higher rigidity. Generally Polyethylene is more expensive than polypropylene – the cheapest of the thermoplastics – though the two share many applications.
PP (Polypropylene)
Polypropylene resin is a usually opaque, low-density polymer with excellent thermoforming and injection molding characteristics. For bottles, It competes primarily against polyethylene and can be made transparent for see-through applications, while polyethylene can only be made translucent, as in milk jugs, for example. Polypropylene cannot match the optical clarity of polymers such as polycarbonate, but it does quite well. Its low viscosity at melt temperatures makes it well suited to extrusion and molding applications, including blow molding.
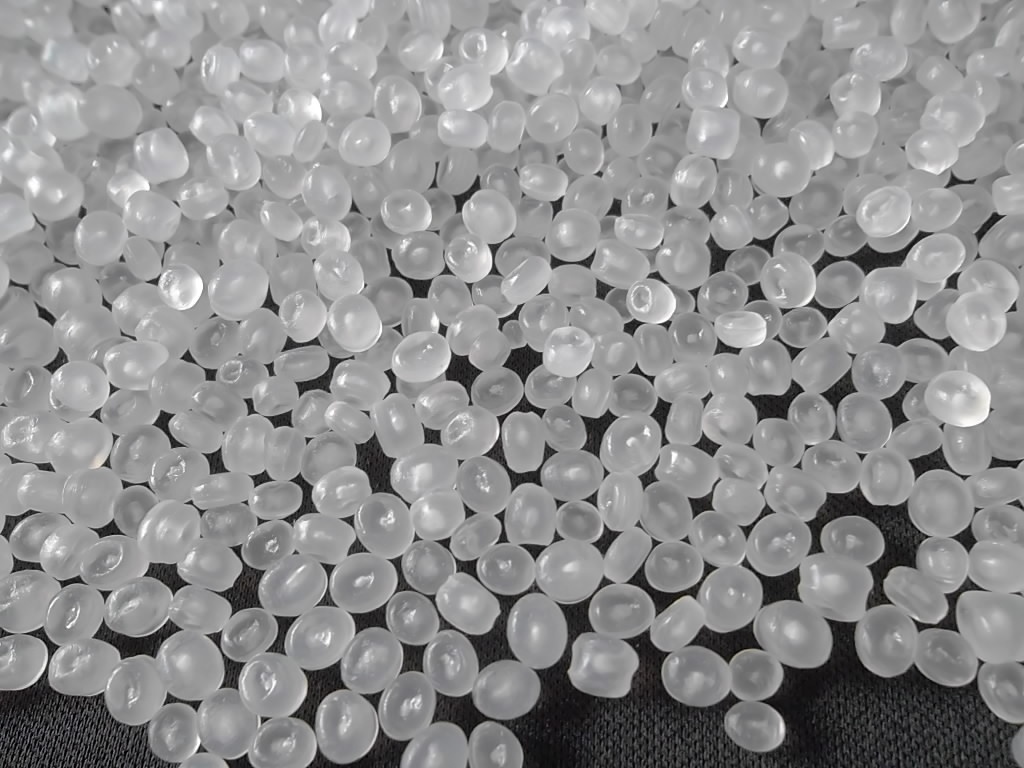
PC (Polycarbonate)
It is a costly material compared with other bottle-making polymers, so its use is restricted primarily to high-end reusable bottles such as nursing bottles or those found on water coolers or in lab settings. The material has excellent optical properties and strength, making it suitable for bottles that must display their contents with the transparency of glass but which also must be able to cope with repeated, and sometimes rough, handling. The material withstands repeated washings and is autoclavable.